Sustainable and Reusable Supply Chain Packaging
Saving You Time, Money and Waste
Global supplier of transit packaging
We design and manufacturing logistics packaging using the latest technology and innovation. Our in house design engineers are constantly innovating to make sure our products perform to the highest standard with the best quality and material usage. Our products are manufactured in our factory in England but shipped all over the world, helping our global partners improve their operational efficiency.
Quality products with lasting impacts
Using Loadhog products within your supply chain will help you to reduce your carbon output. We can work with you to provide a packaging solution which is tailored to your needs, improving your sustainability, while saving time and money. All our products have gone through intense testing to ensure the outcome is high quality, preventing breakages and increasing longevity.
Contact us for a sample
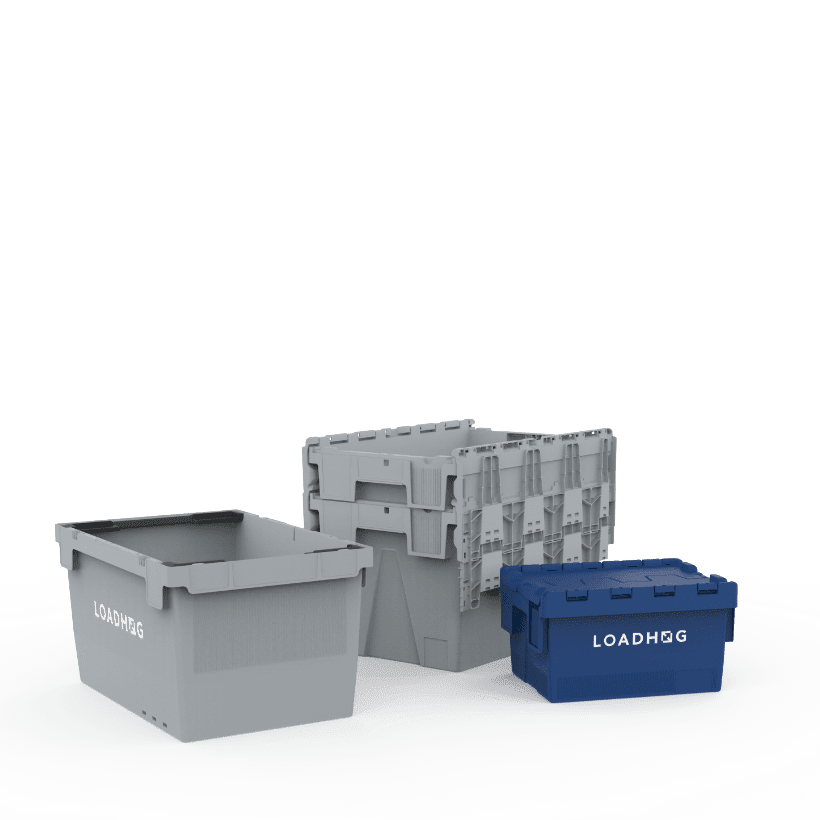
View our digital brochure
View the Loadhog brochure for our full product range
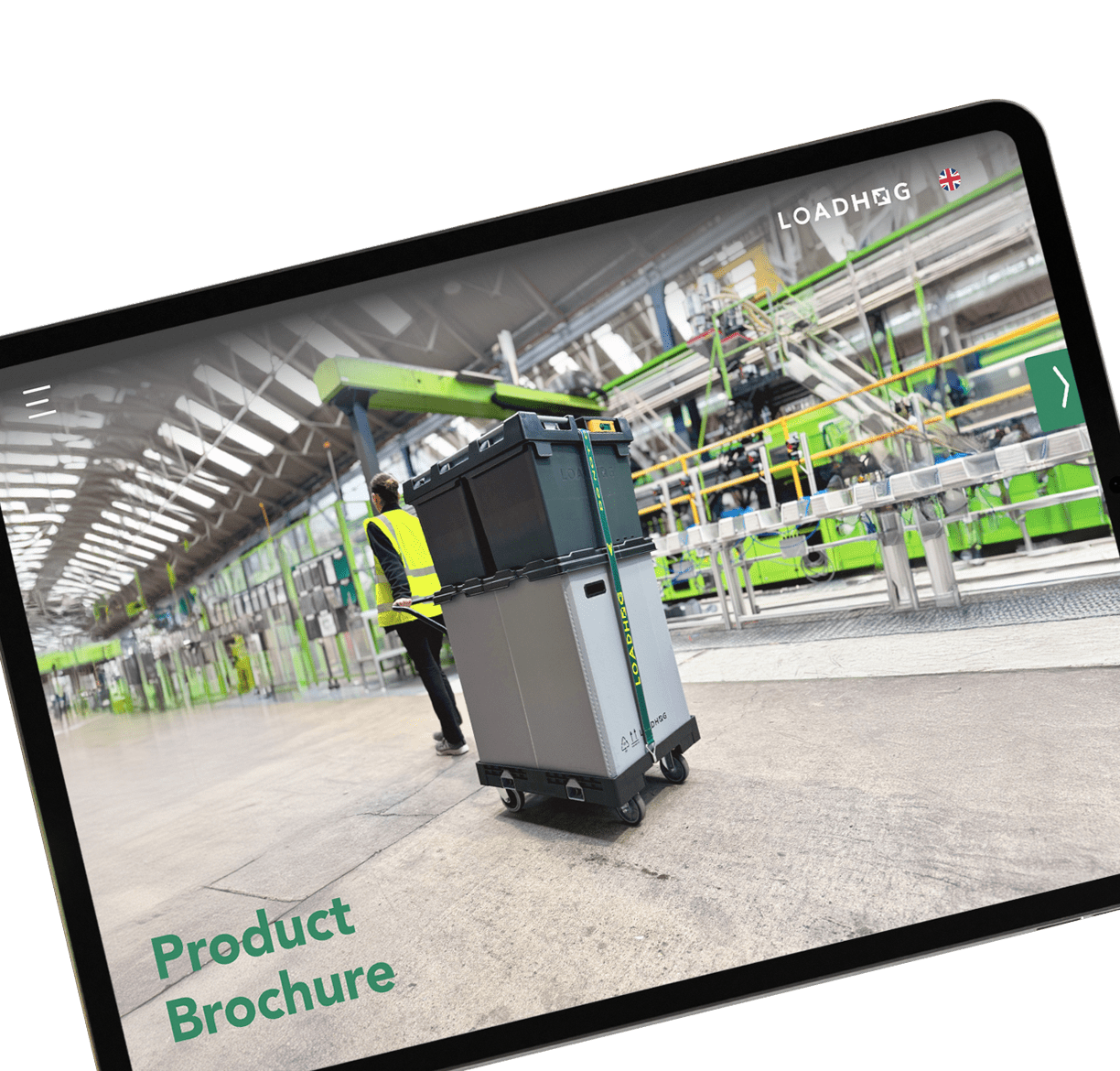
Looking for colour? We offer our products in a range of colours.
Our recycled coloured material avoids Plastic Tax and has been proven to hold the same high quality performance as virgin material.
